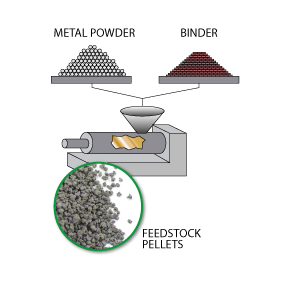
Mixing
Metal powder of fine partical size is mixed with thermoplastic polymer to form a mixture of ingredients konwn as feedstock. The feedstock made into pellets and fed into the molding machine.
The MIM process combines the design flexibility of plastic injection molding with the strength and integrity of wrought metals to offer cost effective solutions for highly complex part geometries. The MIM process is typically explained as four unique processing steps (Mixing, Molding, Debinding and Sintering) to produce a final part that may or may not need final finishing operations.
Metal powder of fine partical size is mixed with thermoplastic polymer to form a mixture of ingredients konwn as feedstock. The feedstock made into pellets and fed into the molding machine.
The feedstock is heated to melt the plastic and molded to the desired shape. The molded parts is known as green part.
The binder is removed thermally by heating to around 400 degree centigrade from the green part, by a debinding process. The debound parts called as brown parts and is brittle and porous.
The brown parts is heated to more than 1200 degree centigrade, in the finale sintering process allowing the part into a dense solid with the elimination of pores. The sintered density is similar to a casting at about 98% of theoretical.
Markets for MIM are broad, and have grown from dental, medical, and firearm applications to include automotive, industrial, sporting, jewelry, hand tools, aerospace, computer, cell phone, and others. Consumer products include watches, latches, eyeglass hinges, and luggage clasps.
Our modern facilities have a combined strength of over 250 skilled engineers, scientists, technicians and manufacturing associates.